Maximize Laser Cutting Efficiency: How Optimyzer Boosts Output by 20%
Manufacturing companies use laser cutting machines mainly to cut pieces out of sheet metal. These versatile machines can produce clean cuts in a wide range of materials, including steel, stainless steel, aluminum and more.
Making fast, clean cuts with a laser machine for each material and each thickness is not an easy task. The machine operator has to select the best values for each setting:
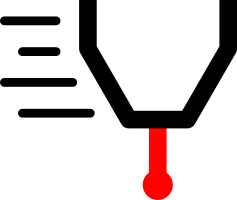
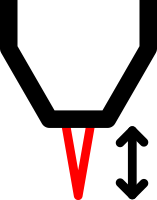
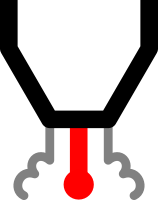

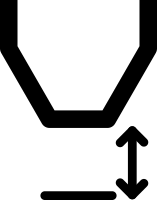
As the cutting head moves over the surface, the focused beam melts the material and the stream of cutting gas blows it away. The feed rate, focus position and laser power affect how much heat gets transferred to the material. The amount of heat absorbed also depends on the type of material, its thickness and the material's temperature. The gas pressure, nozzle distance, nozzle width and nozzle type affect how the molten metal is blown away from the newly created slit. The stream of gas also cools down the metal and can cause or prevent oxidation, depending on the type of gas used. Machine operators need to find a perfect balance of all settings to properly melt the metal and blow it away. This balance creates cuts of excellent quality. A machine operator might spend hours on the machine to find this balance.
The machine's settings not only influence the quality of the cut, but also the costs of running the machine.
Some companies have very good machine operators with years of experience, that know how to tune the settings for each task. Because of the growing problem of the skills shortage, many companies can't find enough skilled operators. In many cases, the operators rely on the default settings recommended by the machine manufacturer. These settings are very conservative and haven't been optimized specifically for the customer's machine, material and demands.
All of it adds up to lost productivity, large costs and a larger carbon footprint.
Find better settings faster with the help of AI
GaussML has developed Optimyzer, an AI-assistant that helps manufacturing companies increase their productivity. Operators get setting suggestions from Optimyzer to try on the machine, and then report back the results. If Optimyzer already has experience on the machine, it leads the operator to better settings within less than 5 experiments.
Manufacturing companies are using Optimyzer to find better settings for flatbed, tube and 3D laser cutting machines. They successfully optimize different machines from the top machine manufacturers: Amada, Bystronic, Prima Power, TRUMPF and many more. Optimyzer helps the operators cut faster, with a better quality and conserve resources for a wide range of materials and thicknesses from 0.15 mm to 25 mm.
Average results from over 100 optimizations
60% faster cuts
23% lower gas consumption
28% higher quality
Done in fewer than 5 experiments
How does it work?
Our customers quickly define their machine using our simple user interface. Operators create a new optimization for the material that they would like to cut. The most commonly optimized settings are the feed rate, gas pressure and focus position. The operator also defines how the machine's performance will be measured and what they want to achieve. Our AI is able to handle subjective quality feedback, like the burr height measured in 0-5 stars. In most cases, the goal for the optimization is to cut as quickly as possible while keeping or improving the cut quality.
The machine operators transfer the suggested settings to the machine and make a cut. After examining the part, they provide a subjective measure for the burr height and, in some cases, also for the kerf quality. No additional sensors or hardware are required, just an operator, a laptop or tablet, and your machine. Optimyzer immediately updates its digital twin of the machine and the material, and provides a new suggestion to try on the machine. The operator can repeat these steps as needed, until they are content with the results.
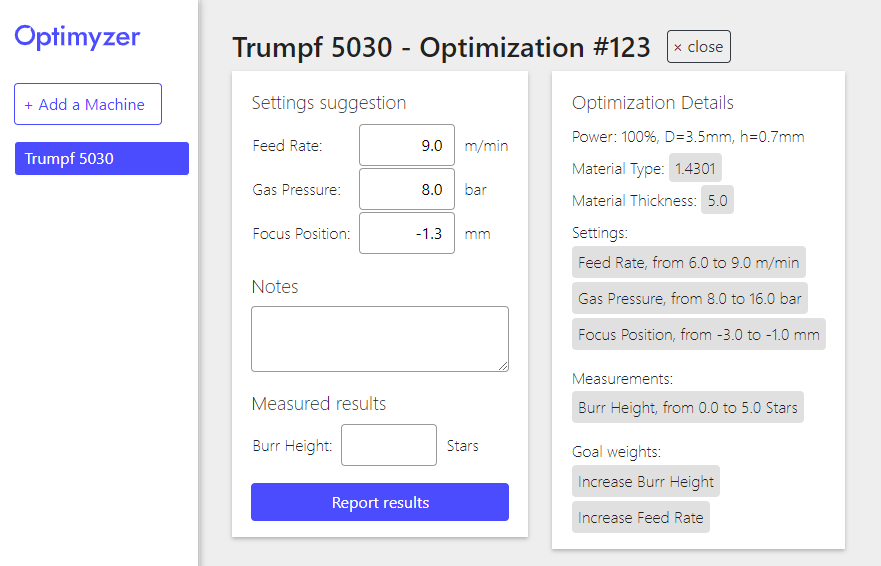
Optimyzer helps the machine operator find the best settings to produce high-quality cuts as quickly as possible. Our customers decide what they want to prioritize for each optimization: speed, quality, resources or a combination of them. After running an optimization, the operator can store the best performing settings on the machine. Each experiment is properly documented and conveniently displayed on a sortable table. This information helps the operator understand which settings worked well and which didn't. The experiments table on Optimyzer remains available, so the operator can later use other good settings that have a higher speed, better quality or use less cutting gas.
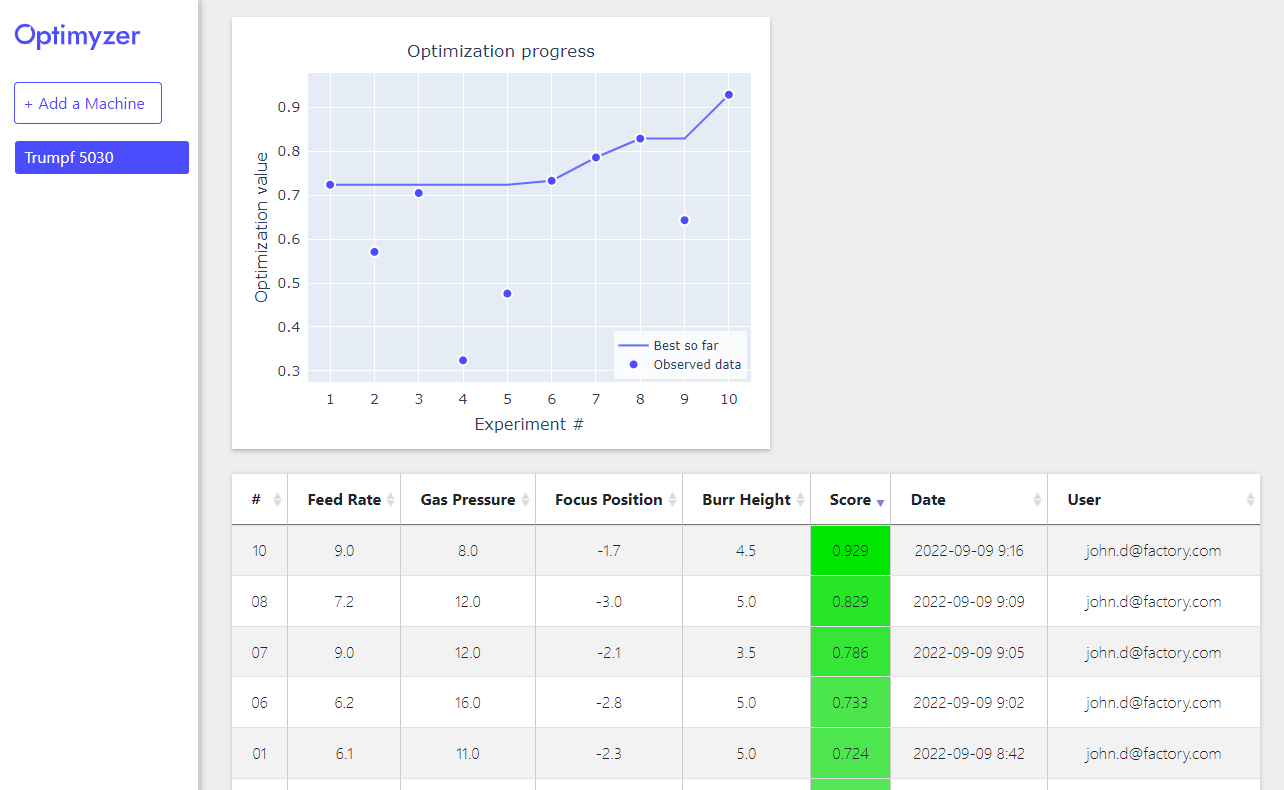
Find out how to increase the efficiency of your laser cutting machines today.
Request a demo